Best Tips About Why DC Motor Instead Of AC

Why Do DC Motors Have Higher Starting Torque Than AC Motors?
DC Motors vs. AC Motors
1. Understanding the Core Difference
Alright, let's untangle this electrical spaghetti. Why do engineers sometimes choose a DC motor instead of an AC motor? It's not just a random pick! The answer, as with most engineering questions, lies in the application. Think of it like choosing between a screwdriver and a wrench. Both tighten things, but one is clearly better for certain nuts and bolts.
AC (Alternating Current) motors are generally cheaper and more efficient for constant-speed applications. They're the workhorses behind your refrigerators, washing machines, and other appliances that just need to hum along at a consistent pace. They're simple to build, reliable, and can handle a decent amount of torque.
But DC (Direct Current) motors shine when you need precise speed control and high starting torque. Imagine a robot arm needing to delicately place components or a conveyor belt that needs to smoothly start and stop. That's where DC motors really strut their stuff. They offer a level of control that AC motors often can't match without adding complex and expensive control systems.
So, the core difference really boils down to control and application. Think constant speed and cost-effectiveness? AC is usually the way to go. Think variable speed, high starting torque, and precision? DC motors are often the better, albeit sometimes more expensive, solution.
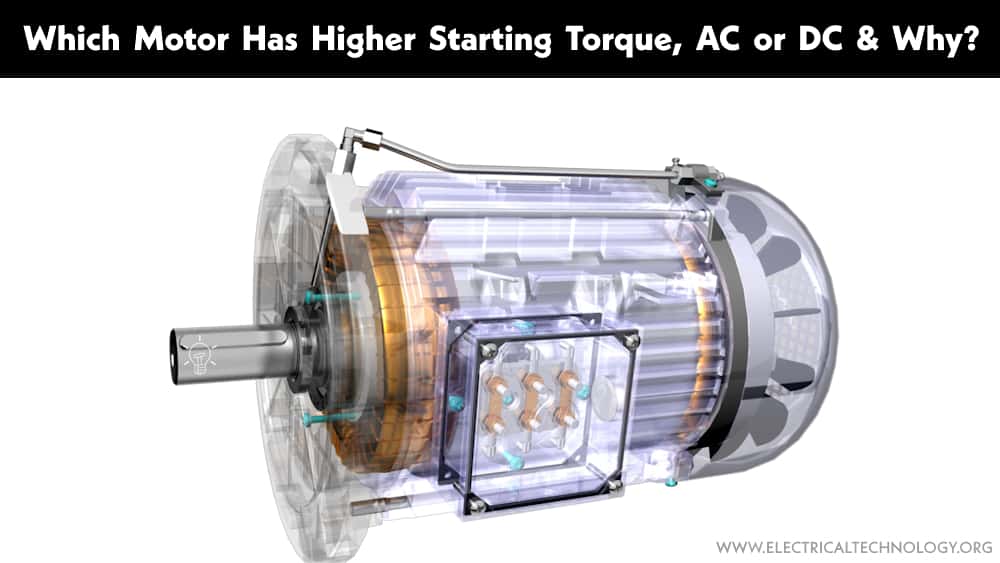
Which Motor Has Higher Starting Torque, AC Or DC And Why?
The Power of Precision
2. Delving Deeper into Speed Control
Let's say you're building a fancy coffee grinder. You want users to be able to select the grind size, from coarse to super-fine. An AC motor might be able to power the blades, but precisely controlling the speed to achieve different grinds becomes tricky. You'd need additional, often complex, electronics to modulate the AC power in a way that allows for accurate speed adjustments.
A DC motor, on the other hand, is naturally easier to control. By simply adjusting the voltage supplied to the motor, you can directly influence its speed. This makes it ideal for applications requiring fine-grained speed regulation. Think of it like the volume knob on your radio — turning it up and down directly changes the output. That level of immediate control is a major advantage for DC motors.
This inherent controllability also extends to torque. High starting torque is critical in applications where the motor needs to overcome inertia or a heavy load right from the get-go. DC motors excel in this area, making them perfect for things like electric vehicle motors or industrial machinery that needs to start under a load.
Essentially, when pinpoint accuracy in speed and torque is paramount, DC motors provide a level of responsiveness that AC motors often struggle to match without significantly more complex (and pricey) accompanying circuitry.

Why Electronic Devices Use DC Supply Instead Of AC
Cost Considerations
3. The Price Tag Tango
Let's be real: money matters! Generally, AC motors are less expensive to manufacture than DC motors, especially the simpler induction types. This is because they have a less complex design and fewer components. For many basic applications, the cost savings alone make AC motors the clear winner.
However, that lower initial cost doesn't always tell the whole story. Remember that coffee grinder? If you absolutely need the precise grind control, you might end up spending more on the extra electronics required to control an AC motor than you would on a simpler DC motor and its associated control circuitry. So, you need to consider the total system cost, not just the motor's price tag.
Maintenance is another factor to consider. DC motors, especially those with brushes, tend to require more maintenance than AC motors. Those brushes wear down over time and need to be replaced. AC induction motors, being largely brushless, are generally more reliable and require less frequent servicing. This can translate to lower long-term operating costs.
Ultimately, the best choice depends on a careful evaluation of your needs, budget, and tolerance for maintenance. There's no universally "better" motor; it's all about finding the right tool for the job (and for your wallet!).

Ac And Dc Difference
Application Spotlight
4. From Robotics to Electric Vehicles
Let's look at some real-world examples where DC motors are the go-to choice. Robotics is a prime example. The precise movements required for robotic arms and automated systems demand the fine speed and torque control that DC motors provide. Imagine a surgical robot — you absolutely need that level of accuracy!
Electric vehicles (EVs) are another major application. While some EVs use AC induction motors, many utilize DC motors (particularly permanent magnet DC motors) for their excellent torque characteristics, especially at low speeds. This allows for rapid acceleration and efficient hill climbing.
Consider adjustable speed drives (ASDs) in industrial settings. These systems often use DC motors to precisely control the speed of pumps, fans, and other equipment. This can significantly improve energy efficiency and process control, leading to cost savings and better performance.
Even smaller applications, like electric wheelchairs and power tools, often rely on DC motors for their controllability and power-to-weight ratio. The ability to efficiently deliver high torque in a compact package makes them ideal for these demanding applications. It's all about that blend of power, control, and size.

7 Reasons Why AC Motors Are More Efficient Than DC (Explained!)
Future Trends
5. The Evolution of Electric Machines
The world of electric motors is constantly evolving. Advancements in materials science, control algorithms, and power electronics are blurring the lines between DC and AC motor capabilities. We're seeing AC motors with increasingly sophisticated control systems that allow them to achieve performance levels previously only attainable with DC motors.
Simultaneously, DC motor technology is also advancing. Brushless DC (BLDC) motors are becoming more prevalent. BLDC motors offer the advantages of DC motors — precise control and high torque — without the maintenance headaches associated with brushes. They're more efficient, more reliable, and have a longer lifespan.
The rise of variable frequency drives (VFDs) is also playing a significant role. VFDs allow you to control the speed and torque of AC motors with much greater precision, making them suitable for a wider range of applications. This is challenging the traditional dominance of DC motors in some areas.
Ultimately, the future is likely to see a convergence of technologies. We'll see both DC and AC motors becoming more sophisticated and versatile, with the choice between them becoming even more application-specific. The key will be to carefully evaluate the specific requirements of each application and select the motor technology that offers the best balance of performance, cost, and reliability. Its not a matter of one replacing the other, but rather them both getting better at what they do best and sometimes even borrowing ideas from each other!
FAQ
6. Quick Answers to Common Inquiries
Here are some frequently asked questions about DC and AC motors to help clear up any remaining confusion:
Q: When should I choose a DC motor over an AC motor?
A: Choose a DC motor when you need precise speed control, high starting torque, or have a battery-powered application. Think robots, electric vehicles, and adjustable speed drives.
Q: Are AC motors always cheaper than DC motors?
A: Generally, yes, AC motors are less expensive to manufacture. However, you need to consider the total system cost, including any additional control circuitry required to achieve the desired performance. Sometimes the extra components needed to control an AC motor will make the total system cost higher than using a DC motor.
Q: What is a brushless DC (BLDC) motor, and why is it better?
A: A BLDC motor is a type of DC motor that doesn't use brushes. This makes it more efficient, more reliable, and require less maintenance than traditional brushed DC motors. They are becoming increasingly popular in many applications.
Q: What are some disadvantages of using DC motor?
A: The DC motors are more expensive, and the brushes need regular replacing, which requires continuous maintainence.