Fine Beautiful Tips About What Are The Disadvantages Of A Closed-loop System

Understanding Closed-Loop Systems
1. The Upside? Precision. The Downside? Potential Headaches.
Closed-loop systems, also known as feedback control systems, are like that super-organized friend who always double-checks everything. They constantly monitor their output and adjust their actions based on the feedback they receive. Think of your home thermostat. It senses the room temperature and then tells the furnace to kick on or off to maintain your desired setting. Sounds pretty amazing, right? And it is, for many applications. However, like anything in life, there are downsides. Let's dive into the potential pitfalls of relying solely on closed-loop control. It's not always the perfect solution, and understanding the drawbacks is key to making informed decisions.
Imagine you're trying to bake a cake using only a closed-loop system. The system monitors the oven temperature and adjusts the heating elements accordingly. But what if the recipe is wrong? Or what if the system is not calibrated correctly? You could end up with a burnt or undercooked cake, no matter how accurately the system maintains the oven temperature. Its a classic case of garbage in, garbage out. So, while closed-loop systems excel at maintaining a specific target, they're utterly dependent on the accuracy of the initial instructions and the reliability of the feedback mechanisms.
And what about unexpected events? Lets say someone accidentally opens the oven door while your cake is baking. The temperature plummets! A closed-loop system will frantically try to compensate, but depending on the responsiveness of the heating elements, the cake could still be ruined. External disturbances can throw a wrench into the best-laid plans of a closed-loop system. This is why it's crucial to consider the environment in which the system operates and to design it to be robust enough to handle potential disruptions.
Furthermore, implementing and maintaining closed-loop systems can be complex and expensive. They require sophisticated sensors, controllers, and actuators, all of which add to the initial cost. And because of their complexity, these systems often require specialized expertise to troubleshoot and repair. This can lead to higher operational costs over the long term. Before committing to a closed-loop solution, its essential to weigh the benefits against the potential costs and complexity.

Overview Of Control System Ppt Download
Increased Complexity and Cost
2. More Parts, More Problems (and More Money)
One of the biggest disadvantages of closed-loop systems is their inherent complexity. Unlike open-loop systems that simply execute a pre-programmed set of instructions, closed-loop systems require a network of sensors, controllers, and actuators working in harmony. This added complexity translates directly into increased costs, both in terms of initial investment and ongoing maintenance. Think of it like upgrading from a basic bicycle to a high-performance racing bike — sure, you might go faster, but there are a lot more components that can break down!
Consider the sensors, for example. These devices are responsible for gathering data about the system's output. They need to be accurate, reliable, and robust enough to withstand the operating environment. High-quality sensors can be quite expensive, and they may require regular calibration or replacement to maintain their accuracy. Then there's the controller, which processes the sensor data and determines the appropriate corrective actions. The controller needs to be powerful enough to handle the computational load, and it may require specialized programming or configuration.
Actuators are the workhorses of the system, responsible for implementing the corrective actions determined by the controller. These devices could be anything from motors and valves to heating elements and pumps. Actuators need to be precise and responsive, and they may require significant power to operate. All of these components add to the overall cost of the system, and they also increase the potential points of failure. A failure in any one of these components can disrupt the entire system, leading to downtime and costly repairs.
Moreover, the added complexity of closed-loop systems often requires specialized expertise to design, implement, and maintain. You might need to hire engineers, technicians, or consultants with specific knowledge of control systems. This can further increase the operational costs. So, while closed-loop systems can offer significant performance advantages, it's crucial to carefully consider the cost implications before making a decision. A simple open-loop system might be a more cost-effective solution in many applications.

Potential for Instability
3. Overshooting, Oscillations, and Runaway Systems
The very feedback mechanism that makes closed-loop systems so effective can also be their Achilles' heel. Under certain conditions, the feedback loop can become unstable, leading to undesirable behaviors like oscillations or even runaway conditions. Imagine you're driving a car with an overly sensitive cruise control system. The system constantly adjusts the throttle to maintain your desired speed, but it overreacts to every little bump or change in gradient. This could lead to a jerky, uncomfortable ride, as the car accelerates and decelerates repeatedly. That's essentially what happens when a closed-loop system becomes unstable.
Instability can arise from a variety of factors, including excessive gain, delays in the feedback loop, or nonlinearities in the system. Excessive gain means that the controller overreacts to small errors, leading to overcorrection and oscillations. Delays in the feedback loop can cause the controller to take corrective actions based on outdated information, which can also lead to oscillations. Nonlinearities, such as saturation or dead zones, can distort the feedback signal and make it difficult for the controller to maintain stability.
In some cases, instability can lead to a runaway condition, where the system's output diverges uncontrollably. Think of a nuclear reactor with a malfunctioning control system. If the control rods fail to properly regulate the nuclear reaction, the reactor temperature could skyrocket, leading to a meltdown. While this is an extreme example, it illustrates the potential consequences of instability in a closed-loop system.
Avoiding instability requires careful design and tuning of the control system. Engineers use a variety of techniques, such as Bode plots and Nyquist diagrams, to analyze the stability of a system and to design controllers that will ensure stable operation. It's also important to consider the operating environment and to design the system to be robust enough to handle potential disturbances. Regular monitoring and maintenance can also help to detect and prevent instability before it becomes a serious problem.

Closed Loop Systems A Deeper Look Arnott Suspension Products
Dependence on Accurate Sensors and Actuators
4. Bad Data In, Bad Performance Out
A closed-loop system is only as good as its sensors and actuators. If these components are inaccurate, unreliable, or poorly calibrated, the entire system can suffer. Imagine you're trying to control the temperature of a chemical reactor using a faulty temperature sensor. The sensor consistently underestimates the actual temperature, causing the control system to overheat the reactor, potentially leading to a dangerous explosion. This highlights the critical importance of ensuring the accuracy and reliability of sensors and actuators in closed-loop systems.
Sensors are responsible for providing feedback about the system's output. They need to be accurate enough to provide meaningful information to the controller. If the sensors are noisy or have a significant bias, the controller will make incorrect decisions, leading to poor performance. Furthermore, sensors need to be reliable and robust enough to withstand the operating environment. They should be able to operate accurately over a wide range of temperatures, pressures, and other environmental conditions. Regular calibration and maintenance are essential to ensure that sensors remain accurate and reliable over time.
Actuators are responsible for implementing the corrective actions determined by the controller. They need to be precise and responsive enough to execute the control commands accurately. If the actuators are sluggish or have a significant dead zone, the system will not be able to respond quickly to changes in the output. Actuators also need to be powerful enough to deliver the required force or energy. If the actuators are undersized, they will not be able to correct for large errors, leading to poor performance. Regular maintenance and inspection are essential to ensure that actuators remain in good working condition.
The choice of sensors and actuators is a critical design decision that should be based on the specific requirements of the application. Factors to consider include accuracy, resolution, range, bandwidth, linearity, reliability, and cost. It's also important to consider the operating environment and to select components that are compatible with the expected conditions. By carefully selecting and maintaining sensors and actuators, you can ensure that your closed-loop system operates accurately and reliably.

Not Always the Best Choice
5. Overkill for Simple Tasks
While closed-loop systems offer numerous advantages, they are not always the best choice. In some cases, a simpler open-loop system may be more appropriate. Using a closed-loop system to control something really simple, such as turning on a light switch at a specific time each day, is just overkill! That's what a simple timer is for. Adding sensors and feedback loops just makes things unnecessarily complex and expensive.
Consider applications where the desired output is well-defined and predictable. For example, if you need to heat a room to a specific temperature, a simple open-loop system with a pre-set heating element may be sufficient. You can determine the appropriate heating level based on the size of the room and the desired temperature. There's no need to add sensors and feedback loops if the system consistently achieves the desired outcome.
Another situation where open-loop systems may be preferable is when the cost of implementing and maintaining a closed-loop system outweighs the benefits. For example, if you need to control the speed of a small fan, a simple open-loop system with a variable resistor may be adequate. Adding a tachometer and a feedback loop would add unnecessary complexity and cost to the system. Sometimes, the added precision of a closed-loop system simply isn't worth the extra expense and effort.
Ultimately, the choice between an open-loop and a closed-loop system depends on the specific requirements of the application. It's important to carefully consider the trade-offs between performance, complexity, and cost before making a decision. In many cases, a simple open-loop system can provide a cost-effective and reliable solution. Don't always assume that a closed-loop system is the best option. Sometimes, less is more!
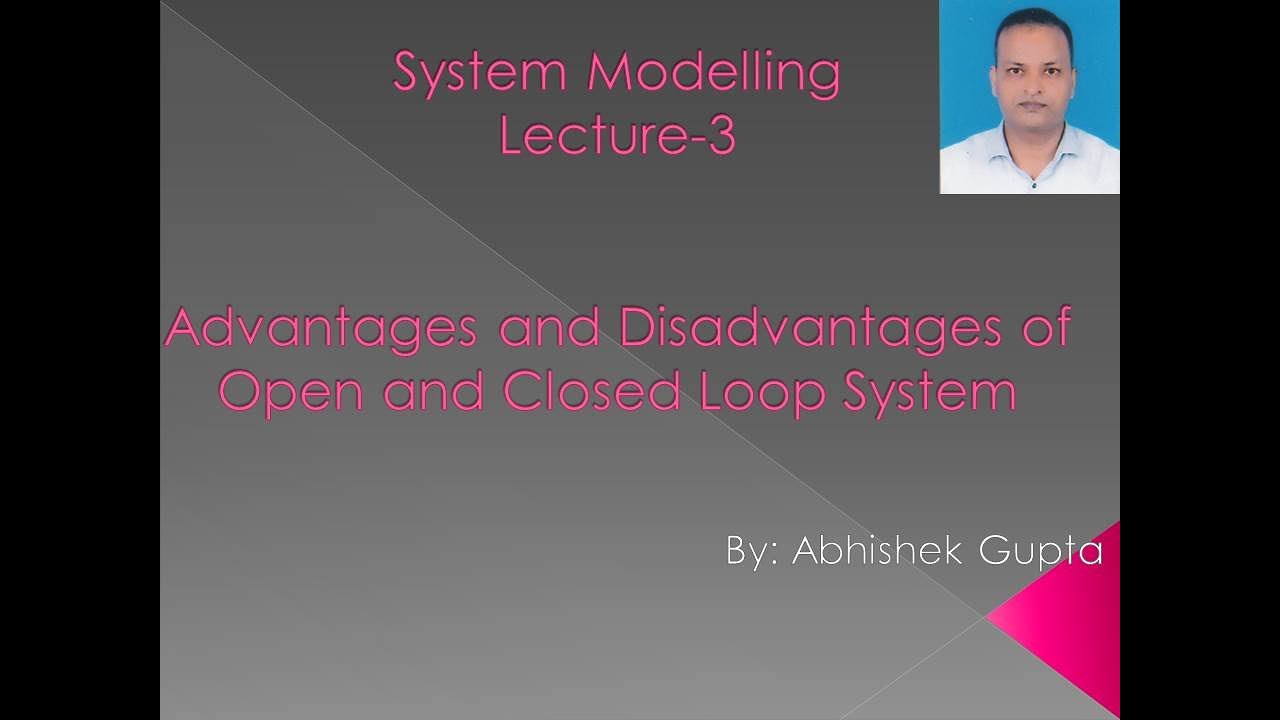
Lec3 Advantages And Disadvantages Of Open Closed Loop System
FAQ about Closed-Loop Systems
6. Your Burning Questions Answered
Still have questions about the downsides of closed-loop systems? Here are some frequently asked questions to help you wrap your head around it all.
Q: Are closed-loop systems always more accurate than open-loop systems?A: Generally, yes, closed-loop systems can be more accurate. But accuracy depends on accurate sensors, proper calibration, and a well-designed control algorithm. A poorly designed closed-loop system can actually be less accurate than a well-designed open-loop system. Its not an automatic win!
Q: What happens if a sensor fails in a closed-loop system?A: If a sensor fails, the controller will receive incorrect data, which can lead to incorrect actions. This can range from degraded performance to system instability and even damage to equipment. Thats why redundancy (having backup sensors) is often used in critical applications.
Q: Is it possible to convert an open-loop system into a closed-loop system?A: Absolutely! It involves adding sensors to measure the output, a controller to process the feedback, and actuators to adjust the input. However, it's essential to carefully consider the costs and benefits before undertaking such a conversion. Sometimes it's just not worth the effort!
Q: How do I know if a closed-loop system is right for my application?A: Consider factors such as the required accuracy, the complexity of the task, the operating environment, and the cost constraints. If you need high accuracy and the task is complex, a closed-loop system is likely the better choice. However, if the task is simple and cost is a major concern, an open-loop system may be sufficient.